Spring Steel Wires
Description
Benefits of Tata Wiron Spring Steel Wire
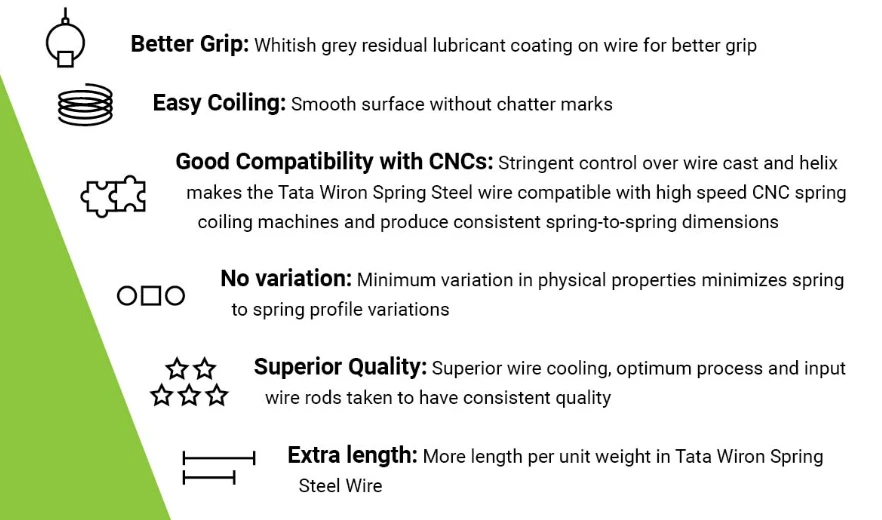
Manufacturing Process
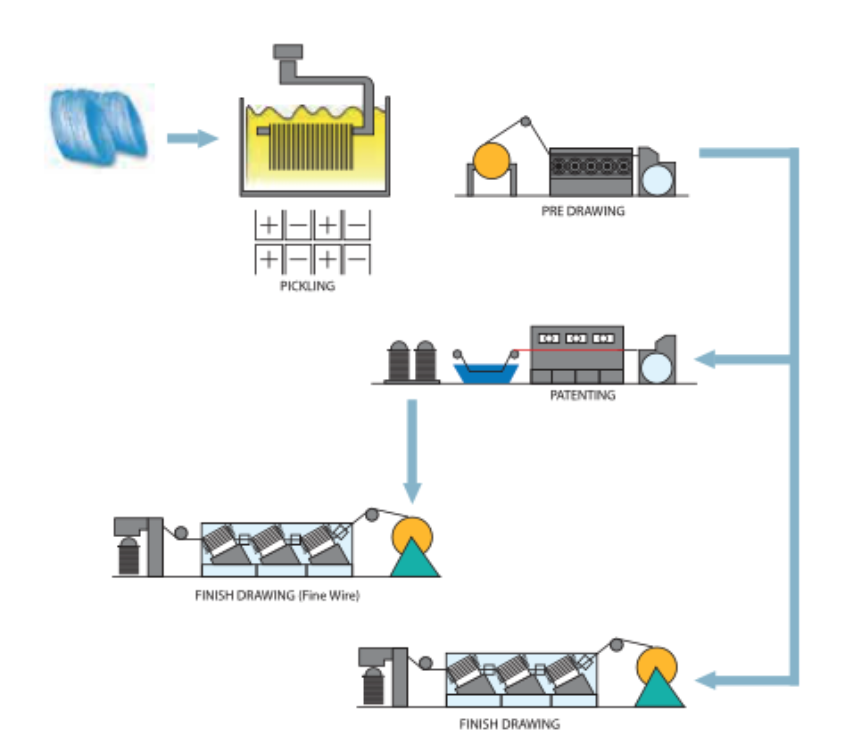
Inbuilt quality checks at all stages of production from steel making to hot rolling and wire drawing
- Carefully designed drawing process to ensure optimum properties
- Uniform coil weight
- Traceability of coils
Attributes tested – Size, Breaking load, Tensile strength, Bends, torsion, and any other customer-specific requirements Quality Report – Each shipment is accompanied by a Mill Test Certificate.
- Raw Material Selection: Start with high-quality raw materials, typically low-carbon or high-carbon steel wire rods. The choice of raw material depends on the desired properties of the final wire product.
- Pickling: The wire rod is cleaned and descaled by immersing it in an acid solution, typically hydrochloric acid or sulfuric acid, to remove surface oxides, scale, and other contaminants. This pickling process prepares the wire rod for subsequent processing by ensuring a clean surface.
- Wire Drawing: After pickling, the wire rod is coated with a lubricant to reduce friction during the drawing process. It is then fed through a series of dies with progressively smaller diameters in a wire drawing machine. This process elongates the wire, reduces its diameter, and improves its surface finish.
- Patenting (optional): After wire drawing, the wire may undergo an annealing process to soften it and relieve internal stresses. Annealing involves heating the wire to a specific temperature and holding it for a certain time before gradually cooling it. This process improves the ductility and machinability of the wire.
- Surface Treatment (Optional): Depending on the application requirements, the wire may undergo various surface treatments such as coating, plating, or passivation to enhance its corrosion resistance, appearance, or other properties.
- Forming and Shaping (Optional): In some cases, the wire may be further processed to achieve specific shapes or forms. This can include processes such as bending, cutting, welding, or coiling to produce wire products with customized configurations.
- Quality Control: Throughout the manufacturing process, quality control measures are implemented to ensure that the wire meets the specified dimensional tolerances, mechanical properties, and surface quality requirements. Inspection methods may include dimensional measurement, tensile testing, surface inspection, and chemical analysis.
Applications
Spring steel wires, known for their high yield strength, resilience, and elasticity, are utilized in a wide range of applications where these properties are critical. Here are some common applications:
- Spring steel wires are extensively used in automotive suspension systems, including coil springs, leaf springs, and stabilizer bars, due to their ability to withstand repeated loading cycles and maintain shape under heavy loads.
- These wires are employed in the manufacturing of various industrial machinery components such as clutch springs, valve springs, conveyor belt springs, and machinery vibration dampers due to their resilience and durability.
- Spring steel wires find application in agricultural machinery for producing components like harrow tines, cultivator springs, and hay rake teeth, where resilience and resistance to bending are essential.
- In the construction industry, spring steel wires are used in the production of concrete reinforcement wires, pre-stressed concrete structures, and suspension bridge cables due to their high tensile strength and ability to maintain structural integrity under tension.
- Spring steel wires are widely used in the manufacturing of mattress springs, including coil springs and Bonnell springs, to provide support, comfort, and resilience to mattresses and upholstered furniture.
- These wires are utilized in the production of various mechanical springs, including tension springs, compression springs, torsion springs, and extension springs, used in diverse applications such as locks, door handles, switches, and industrial machinery.
- Spring steel wires find application in the electrical industry for producing components such as electrical contacts, connectors, and switches due to their conductivity, resilience, and ability to maintain electrical contact under pressure.
- Spring steel wires are used in the manufacturing of medical devices such as surgical instruments, catheters, and orthodontic appliances due to their biocompatibility, resilience, and ability to withstand sterilization processes.
- Spring steel wires are employed in various consumer goods such as furniture, bicycles, toys, and sporting goods for producing components like springs, clips, hooks, and fasteners due to their strength, elasticity, and durability.
- Spring steel wires are used in defense and aerospace applications for producing components such as parachute springs, aircraft landing gear, missile components, and weapon systems due to their high strength-to-weight ratio and reliability under extreme conditions.
We stock Spring steel wires as per the specifications below.
Coil Specifications:
Grade | SM/DM | SH/DH |
Size Range | 0.35- 13.00 | 0.35-9.50 |
Standards | IS | BS | DIN | |
Spring Steel | IS 4454- Part 1 | 5216 | DIN: 17223 Part 1 | |
Year | 1981 | 2001 | N/A | 1998 & 1984 |
Grade 1,2, 3 | SL, SM,SH, DM,DH | Grade 1,2, 3 | Grade A,B, C |
Size (mm) | Weight (kg) | Min Coil ID (mm) | Max Coil OD (mm) | Packing |
1.60 – 3.00 | 350 – 1100 | 500 | 900 | Oil
dipped +
Poluthen
e + Jute
or HDPE
Rusto
Paper + Polythene
+ Jute or
HDPE |
3.10 – 6.00 | 350 – 1000 | 650 | 1200 | |
6.00 – 14.00 | 500 – 1000 | 700 | 1400 |
TABLE 1 SPRING WIRE GRADES (CLAUSE 5) | ||||
Tensile Strength | Static Duty | Diameter Range | Dynamic Duty | Diameter Range |
(mm) | (mm) | |||
1 | 2 | 3 | 4 | 5 |
Low tensile strength | SL | 1.00-10.00 | – | – |
Medium tensile strength | SM | 0.30-20.00 | DM | 0.08-20.00 |
High tensile strength | SH | 0.30-20.00 | DH | 0.05-20.00 |
Note – For specific applications, other tensile strength requirements may be agreed |
TABLE 2 Chemical Composition (CLAUSE 7.1, 7.1.1 and 7.2, 7.2.1) | ||||||
Grade | Constituent Percent | |||||
C | Si | Mn | S | P | Cu | |
Max | Max | Max | ||||
1 | 2 | 3 | 4 | 5 | 6 | 7 |
SL, SM,SH | 0.35-1.00 | 0.10-0.30 | 0.30-1.20 | 0.030 | 0.030 | 0.20 |
DM , DH | 0.45-1.00 | 0.10-0.30 | 0.30-1.50 | 0.020 | 0.025 | 0.12 |
Table 4 Diameter Tolerance for Coiled Wire (CLAUSE 9.1 and 9.2 ) | |||||||
Nominal Diameter of Wire | Tolerance (+-) | Nominal Diameter of Wire | Tolerance (+-) | ||||
Class A | Class B | Class A | Class B | ||||
Over | Up to and Including | Over | Up to and Including | ||||
mm | mm | mm | mm | mm | mm | mm | mm |
1 | 2 | 3 | 4 | 1 | 2 | 3 | 4 |
– | 0.05 | 0.003 | – | 1.78 | 2.78 | 0.025 | 0.030 |
0.05 | 0.09 | 0.003 | – | 2.78 | 4.00 | 0.030 | 0.030 |
0.09 | 0.17 | 0.004 | – | 4.00 | 5.45 | 0.035 | 0.035 |
0.17 | 0.26 | 0.005 | – | 5.45 | 7.10 | 0.040 | 0.040 |
0.26 | 0.37 | 0.006 | 0.010 | 7.10 | 9.00 | 0.045 | 0.045 |
0.37 | 0.65 | 0.008 | 0.012 | 9.00 | 10.00 | 0.050 | 0.050 |
0.65 | 0.8 | 0.01 | 0.015 | 10.00 | 11.10 | 0.070 | 0.070 |
0.8 | 1.01 | 0.015 | 0.020 | 11.10 | 14.50 | 0.080 | 0.080 |
1.01 | 1.78 | 0.020 | 0.025 | 14.50 | 18.30 | 0.090 | 0.090 |
18.30 | 20.00 | 0.100 | 0.100 | ||||
NOTES | |||||||
1 Class A tolerance is intended for wire grades SH, DM and DH | |||||||
2 Class B tolerance is intended for wire grades SL and SM |
Table 5 Tensile Strength Requirements ( Clause 10.1) | |||||
Nominal Diameter | Tensile Strength for Grades, Mpa | ||||
of Wire, mm | SL | SM | DM | SH | DH |
1 | 2 | 3 | 4 | 5 | 6 |
0.05 | – | – | – | – | 2800 – 3520 |
0.06 | – | – | – | – | 2800 – 3520 |
0.70 | – | – | – | – | 2800 – 3520 |
0.08 | – | – | 2780 – 3100 | – | 2800 – 3480 |
0.09 | – | – | 2740 – 3060 | – | 2800 – 3430 |
0.10 | – | – | 2710 – 3020 | – | 2800 – 3380 |
0.11 | – | – | 2690 – 3000 | – | 2800 – 3350 |
0.12 | – | – | 2660 – 2960 | – | 2800 – 3320 |
0.14 | – | – | 2620 – 2910 | – | 2800 – 3250 |
0.16 | – | – | 2570 – 2860 | – | 2800 – 3200 |
0.18 | – | – | 2530 – 2820 | – | 2800 – 3160 |
0.20 | – | – | 2500 – 2790 | – | 2800 – 3110 |
0.22 | – | – | 2470 – 2760 | – | 2770 – 3080 |
0.25 | – | – | 2420 – 2760 | – | 2720 – 3010 |
0.28 | – | – | 2390 – 2670 | – | 2680 – 2970 |
0.30 | – | 2370 – 2650 | 2370 – 2650 | 2660 – 2940 | 2660 – 2940 |
0.32 | – | 2350 – 2630 | 2350 – 2630 | 2640 – 2920 | 2640 – 2920 |
0.34 | – | 2330 – 2600 | 2330 – 2600 | 2610 – 2890 | 2610 – 2890 |
0.36 | – | 2310 – 2580 | 2310 – 2580 | 2590 – 2870 | 2590 – 2890 |
0.38 | – | 2290 – 2560 | 2290 – 2560 | 2570 – 2850 | 2570 – 2850 |
0.40 | – | 2270 – 2550 | 2270 – 2550 | 2560 – 2830 | 2570 – 2830 |
0.43 | – | 2250 – 2520 | 2250 – 2520 | 2530 – 2800 | 2570 – 2800 |
0.45 | – | 2240 – 2500 | 2240 – 2500 | 2510 – 2780 | 2570 – 2780 |
0.48 | – | 2220 – 2480 | 2240 – 2500 | 2490 – 2760 | 2570 – 2760 |
0.50 | – | 2200 – 2470 | 2200 – 2470 | 2480 – 2740 | 2480 – 2740 |
0.53 | – | 2180 – 2450 | 2180 – 2450 | 2460 – 2720 | 2460 – 2720 |
0.56 | – | 2170 – 2430 | 2170 – 2430 | 2440 – 2700 | 2440 – 2700 |
0.60 | – | 2140 – 2400 | 2140 – 2400 | 2410 – 2670 | 2410 – 2670 |
0.63 | – | 2130 – 2380 | 2130 – 2380 | 2390 -2650 | 2390 – 2650 |
0.65 | – | 2120 – 2370 | 2120 – 2370 | 2380 – 2640 | 2380 – 2640 |
0.70 | – | 2090 – 2350 | 2090 – 2350 | 2360 – 2610 | 2360 – 2610 |
0.75 | – | 2070 – 2330 | 2070 – 2330 | 2340 – 2580 | 2340 – 2580 |
0.80 | – | 2050 – 2350 | 2050 – 2350 | 2310 – 2560 | 2310 – 2560 |
0.85 | – | 2030 – 2280 | 2030 – 2280 | 2290 – 2530 | 2290 – 2530 |
0.90 | – | 2010 – 2260 | 2010 – 2260 | 2270 – 2510 | 2270 – 2510 |
0.95 | – | 2000 – 2240 | 2000 – 2240 | 2250 -2490 | 2250 -2490 |
1.00 | 1720 – 1970 | 1980 – 2220 | 1980 – 2220 | 2230 – 2470 | 2230 – 2470 |
1.05 | 1710 – 1950 | 1960 – 2220 | 1960 – 2220 | 2210 – 2450 | 2210 – 2450 |
1.10 | 1690 – 1940 | 1950 -2190 | 1950 -2190 | 2200 – 2430 | 2200 – 2430 |
1.20 | 1670 – 1910 | 1920 -2160 | 1920 -2160 | 2470 – 2400 | 2470 – 2400 |
1.25 | 1660 – 1900 | 1910 – 2130 | 1910 – 2130 | 2140 – 2380 | 2140 – 2380 |
1.30 | 1640 – 1890 | 1900 – 2310 | 1900 – 2310 | 2140 – 2370 | 2140 – 2370 |
1.40 | 1620 – 1860 | 1870 – 2100 | 1870 – 2100 | 2110 – 2340 | 2110 – 2340 |
1.50 | 1600 – 1840 | 1850 – 2080 | 1850 – 2080 | 2090 – 2310 | 2090 – 2310 |
1.60 | 1590 – 1820 | 1830 – 2050 | 1830 – 2050 | 2060 – 2290 | 2060 – 2290 |
1.70 | 1570 – 1800 | 1810 – 2030 | 1810 – 2030 | 2040 – 2260 | 2040 – 2260 |
1.80 | 1550 – 1780 | 1790 – 2010 | 1790 – 2010 | 2020 – 2240 | 2020 – 2240 |
1.90 | 1540 – 1760 | 1770 – 1990 | 1770 – 1990 | 2000 – 2220 | 2000 – 2220 |
2.00 | 1520 – 1750 | 1760 – 1970 | 1760 – 1970 | 1980 – 2200 | 1980 – 2200 |
2.10 | 1510 – 1730 | 1740 – 1960 | 1740 – 1960 | 1970 – 2180 | 1970 – 2180 |
2.25 | 1490 – 1710 | 1720- 1930 | 1720- 1930 | 1940 – 2150 | 1940 – 2150 |
2.40 | 1470 – 1690 | 1700 – 1910 | 1700 – 1910 | 1920 – 2130 | 1920 – 2130 |
2.50 | 1460 – 1680 | 1690 – 1890 | 1690 – 1890 | 1900 – 2110 | 1900 – 2110 |
2.60 | 1450 – 1660 | 1670 – 1880 | 1670 – 1880 | 1890 – 2100 | 1890 – 2100 |
2.80 | 1420 – 1640 | 1650 – 1850 | 1650 – 1850 | 1860 – 2070 | 1860 – 2070 |
3.00 | 1410 – 1620 | 1630- 1830 | 1630- 1830 | 1840 – 2040 | 1840 – 2040 |
3.20 | 1390 – 1600 | 1610 – 1810 | 1610 – 1810 | 1820 – 2020 | 1820 – 2020 |
3.40 | 1370 – 1580 | 1590 – 1780 | 1590 – 1780 | 1790 – 1990 | 1790 – 1990 |
3.60 | 1350 – 1560 | 1570 -1760 | 1570 -1760 | 1770 – 1970 | 1770 – 1970 |
3.80 | 1340 – 1540 | 1550 – 1740 | 1550 – 1740 | 1750 – 1950 | 1750 – 1950 |
4.00 | 1320 – 1550 | 1530 – 1730 | 1530 – 1730 | 1740 – 1930 | 1740 – 1930 |
4.25 | 1310 – 1500 | 1510 – 1700 | 1510 – 1700 | 1710 – 1900 | 1710 – 1900 |
4.50 | 1290 – 1490 | 1500 -1680 | 1500 -1680 | 1690 – 1880 | 1690 – 1880 |
4.75 | 1270 – 1470 | 1480 – 1670 | 1480 – 1670 | 1680 – 1840 | 1680 – 1840 |
5.00 | 1260 – 1450 | 1460 – 1650 | 1460 – 1650 | 1660 – 1830 | 1660 – 1830 |
5.30 | 1240 – 1430 | 1440 – 1630 | 1440 – 1630 | 1640 – 1820 | 1640 – 1820 |
5.60 | 1230 – 1420 | 1430 -1610 | 1430 -1610 | 1620 – 1800 | 1620 – 1800 |
6.00 | 1210 – 1390 | 1400 – 1580 | 1400 – 1580 | 1590 – 1770 | 1590 – 1770 |
6.30 | 1190 – 1380 | 1390 – 1560 | 1390 – 1560 | 1570 – 1750 | 1570 – 1750 |
6.50 | 1180 – 1370 | 1380 – 1550 | 1380 – 1550 | 1560 – 1740 | 1560 – 1740 |
7.00 | 1160 – 1340 | 1350 – 1530 | 1350 – 1530 | 1540 – 1710 | 1540 – 1710 |
7.50 | 1140 – 1320 | 1330 – 1500 | 1330 – 1500 | 1510 – 1680 | 1510 – 1680 |
8.00 | 1120 – 1300 | 1310 – 1480 | 1310 – 1480 | 1490 – 1660 | 1490 – 1660 |
8.50 | 1110 – 1280 | 1290 – 1460 | 1290 – 1460 | 1470 – 1630 | 1470 – 1630 |
9.00 | 1090 – 1260 | 1270 – 1440 | 1270 – 1440 | 1450 – 1610 | 1450 – 1610 |
9.50 | 1070 – 1250 | 1260 – 1420 | 1260 – 1420 | 1430 – 1590 | 1430 – 1590 |
10.00 | 1060 – 1230 | 1240 – 1400 | 1240 – 1400 | 1410 – 1570 | 1410 – 1570 |
10.50 | – | 1230 – 1380 | 1230 – 1380 | 1390 – 1550 | 1390 – 1550 |
11.00 | – | 1210 – 1370 | 1210 – 1370 | 1380 – 1530 | 1380 – 1530 |
12.00 | – | 1180 – 1340 | 1180 – 1340 | 1350 – 1500 | 1350 – 1500 |
12.50 | – | 1170 – 1320 | 1170 – 1320 | 1330 – 1480 | 1330 – 1480 |
13.00 | – | 1160 – 1310 | 1160 – 1310 | 1320 – 1470 | 1320 – 1470 |
14.00 | – | 1130 – 1280 | 1130 – 1280 | 1290 – 1440 | 1290 – 1440 |
15.00 | – | 1110 – 1260 | 1110 – 1260 | 1270 – 1410 | 1270 – 1410 |
16.00 | – | 1090 – 1230 | 1090 – 1230 | 1240 – 1390 | 1240 – 1390 |
17.00 | – | 1070 – 1210 | 1070 – 1210 | 1220 – 1360 | 1220 – 1360 |
18.00 | – | 1050 – 1190 | 1050 – 1190 | 1200 – 1340 | 1200 – 1340 |
19.00 | – | 1030 – 1170 | 1030 – 1170 | 1180 – 1320 | 1180 – 1320 |
20.00 | – | 1020 – 1150 | 1020 – 1150 | 1160 – 1300 | 1160 – 1300 |
Table 6 Torsion Test Requirements (Clause 10.3.3) | ||||||||
Nominal Diameter of wire, mm | Minimum Number of Twistsfor Grades | |||||||
Over | Up to and Including | SL,SM & SH | DM & DH | |||||
(1) | (2) | (3) | (4) | |||||
0.69 | 1.40 | 20 | 25 | |||||
1.40 | 2.00 | 18 | 22 | |||||
2.00 | 3.50 | 16 | 20 | |||||
3.50 | 6.00 | 14 | 18 | |||||
6.00 | 8.00 | 7 | 9 | |||||
8.00 | 10.00 | 5 | 7 | |||||
1) For Guidance only. |